ISOのパフォーマンス評価と監査 第5講座~不適合報告書の書き方と監査手順~
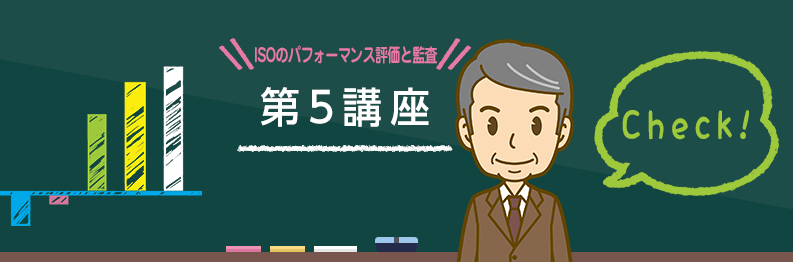
不適合報告書の監査所見の書き方
不適合報告書の監査所見の書き方で問題のある事例です。
事例1:「最終検査で検査者は限度見本を使用していませんでした。」
この表現では「いつ、なにを」が不明確であり、監査基準が記載されていないので、不適合報告書の書き方は次のようにするとよいでしょう。
⇒「QC工程図(X-00X)では、最終検査で限度見本を使用することになっています。3月10日の監査の折り、対象製品Cで検査者Aは限度見本を使用していませんでした。」
事例2:「倉庫管理手順では部品は先入・先出を行うこととなっていますが、5月10日受入の部品が10個あるにも関わらず、5月20日受入の部品20個を使用していました。」
この記述では、部品名の明記がされていないなど一部の情報が不十分ですので、不適合報告書の書き方は次のようにするとよいでしょう。
⇒「倉庫管理手順(Q-XX)では部品は先入・先出を行うこととなっていますが、部品Aは5月10日受入の部品が10個あるにも関わらず、5月20日受入の部品を20個使用していたことが管理表に記入されていました。」
修正及び是正処置の目的は次のとおりですので、フォローアップ監査では処置の結果の状態を確認します。
修正とは、不適合状況を適合に戻すことです。見つかった不適合について、現象そのものを適合した状態に戻し、とりあえず問題をなくすということです。
是正処置とは、再度不適合が発生しないような仕組みを構築することです。不適合の真の要因を調査し特定を行って取り除き、指摘された不適合が二度と起きないような仕組みを作るということです。
現象を原因と勘違いしていることは、原因の特定でよくある悪い例です。
●不適合:作業手順どおりに作業をしていませんでした。
原因:手順が理解されていませんでした。 対策:作業標準に手順を追加します。
⇒問題点:「手順が理解されていない」は現象です。なぜ手順が理解されていなかったのかの原因が追究されていないので、手順を追加する是正を行っています。
●不適合:作成することになっている限度見本が作成されていませんでした。
原因:限度見本がなくても作業に支障がありませんでした。 対策:限度見本を作成しました。
⇒問題点:作業に支障がなければ本来限度見本は必要なかったのですが、なぜ作成することになったのかの調査が行われていません。
●不適合:記録が作成されていませんでした。
原因:作成するのを忘れました。 対策:担当者に忘れずしっかりやるように強く言いました。
⇒問題点:「作成を忘れた」は現象です。なぜ忘れたのかについての原因が追究されていないので安易な処置になっています。
●不適合:検査ミスがありました。
原因:Aさんが検査手順を間違えました。 対策:Aさんの教育を行います。
⇒問題点:「検査手順を間違えた」は現象です。なぜ間違えたのかの原因が追究されていないため安易な処置になっています。
真の原因の特定とは、根本原因を見極めることですが、原因は必ずしも一つとは限りません。マネジメントシステムの各要素間の相互作用から問題が起こることもありますので、直接原因だけでなく、間接原因の追究が必要です。原因の特定と対策を検討する方法として、窓分析を推奨します。

パフォーマンス評価監査の所見
パフォーマンス評価監査の所見の事例です。
事例状況:製造課では、品質方針の達成をするために今年度の品質目標を製造工程内不良率2%以下と決めて、月次管理を行っていました工程内検査の不良率を目視にて確認したところ、4月から今月までの6ヶ月間は1%台と目標を達成していましたが、目標設定がない最終検査結果を確認したところ、最終検査での不良品数は4月からの6ヶ月はそれまでの6ヶ月よりも増加していました。工程内を目視する検査員は4人、そのうち2人が4月に新たに任命されています。
最終検査で不良品数が増えていたことにより、新任検査員に対する再教育・訓練を行うとされています。なお、品質方針の当年度の重要課題は「生産性の向上」です。
以下はパフォーマンス評価監査に関する所見の記載例です。
事実報告:製造課では今年度の品質目標数値を、工程内不良率2%以下と定め、月次管理を行うこととしています。目視による工程内検査における不良率を確認したところ、4月から今月までの6ヶ月間は1%台と達成していました。目視検査の検査員は、4人のうち2人が4月に新しく任命されていました。最終検査機能を確認したところ目標設定はなく、また結果は不良品数がそれまでの6ヶ月よりも増えていました。これにより是正処置として新任の再教育・訓練をするとされています。
監査基準:ISO9001:2015 6.2.1「関連する機能、階層及びプロセスにおいて品質目標を確立しなければならない。」品質目標「工程内不良率2%以下」品質方針の重点課題「生産性の向上」
指摘事由:最終検査結果に関連するプロセスの品質目標の設定がありません。目視による工程内検査における不良率が4月から今月までの6ヶ月間1%台と目標を達成しているにも関わらず、最終検査における不良品数の増加がありましたが、増加の理由及び双方の相互関係についての究明がされていません。
パフォーマンス評価のための監査手順
このような報告に至るためのパフォーマンス評価のための監査手順をまとめました。
- 対象部署について文書をレビューしプロセス構成要素を解析して理解します。
- 基本的な固有知・固有技術、及び管理技術を理解します。
- 重点課題から問題意識を持ち質問事項リストを作成します。
- 面談での質問は用意した質問にとどまらず、調査した文書、担当者による回答、監査で出会った事柄、見出した事実について5W1Hのどれかで脈絡のある深く堀り込む質問をして、じっくり実態の情報を収集します。
- プロセス監査で実施状況をじっくりと監査してつぶさに把握します。
- どのようなアプローチの結果での良し悪しなのかを、トレースバックします。
- プロセスのアウトプットからその機能と能力を評価します。
- 監査所見や監査報告書の作成では、論理的な根拠を明確にするために、誰が見てもわかりやすく、理解しやすいように順序立てて記述します。
- 対象部署が、要求した是正課題の真の原因の除去が出来ているかをフォローアップします。
パフォーマンス評価のための監査とは、いかに専門的な技術が必要かということがお分かりかと思います。こうした監査をして初めて、経営方針に対して支援ができる内部監査になると言えます。
当社では、このような監査を継続支援において提供し、顧客企業の発展に寄与いたします。

ISOプロでは月額4万円から御社に合わせたISO運用を実施中
ISOプロではISO各種の認証取得から運用まで幅広くサポートしております。
また、マニュアル作成など御社に合わせたムダのない運用を心がけており、既に認証を取得しているお客様においてもご提案しております。
サポート料金においても新プランを用意し、業界最安級の月額4万円からご利用いただけます。
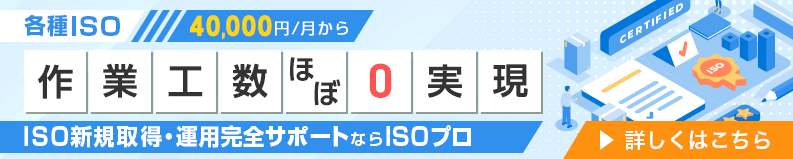
こんな方に読んでほしい